Switch Point Heating Elements
Energy Efficient Flat Heaters
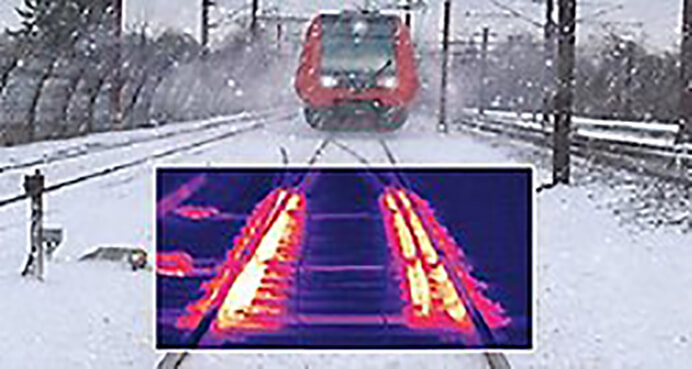
The flat switch heater method of electric heating is the most energy efficient means of electric switch heating. There are different types of electric switch heaters, but the best of these electric heaters are non-coiled flat heaters. They have the most efficient thermal conductivity to the rail since they are flat, have never been coiled, and retain no coiled memory. The flat heater has a much greater thermal conductive profile than round tubular heaters—typically 15% surface area contact for round heaters vs. 40% surface area contact for flat heaters. These numbers assume no coiling and no obstruction on the rail: a contiguous straight run down the rail.
The NIBE Element Railway Solutions electric heaters are designed to be energy efficient heaters that have a maximum thermal conductivity to the rail. Optimal thermal conductivity is achieved through delivering the heaters straight, without coiling, so they have no coiled memory. Coiled memory will never be able to be remedied and will leave inefficient heating gaps to the rail. The construct of the flat heaters is designed around helix elements that produce the heat. These helix elements are completely encapsulated in a highly compressed magnesium oxide. The connections of these flat heaters are completely sealed so there is no danger of water intrusion.
The NIBE Element Railway Solutions flat heater has the slimmest profile of any flat heater. This allows the heater to easily fit in the gaps of track braces without removal of any hardware. In fact, the profile is so slim, we can fit two heaters in the gap of a Pettibone track brace.
We provide stainless steel “knock on” clips that wrap around the rail and can be easily tapped on or off of the rail—no drilling or special tools are required.
Although we have noted that the heaters are delivered straight, they can be bent at the factory to accommodate special applications. Our flat heaters come in wattages of 100 watts/foot to 300 watts/foot in lengths from 4 feet to 24 feet. The thermal conductivity of the flat heater, without coiling, has an equivalent wattage factor of approximately 60% more conductive heat than a round tubular heater. This means that a flat heater that generates 250 watts/foot will have a thermal conductive equivalent to a round tubular heater at 400 watts/foot.
NIBE Element Railway Solutions produces and markets two types of flat heaters that support the lengths and wattages referenced above:
Monel 400 Sheathed Flat Heaters
The Monel 400 sheathed heaters are truly unique heaters. In addition to the NIBE Element Railway Solutions switch point heating technology design, the heaters are sheathed in a Monel 400 alloy sheathing.
The Monel 400 alloy is the perfect metal for harsh salt environments such as rail. Monel 400 is near impervious to salt and most chemicals—it is used in undersea applications for cabling.
The ability to stand up to these harsh environments has allowed us to offer a 10-year warranty on the switch point heaters with the Monel 400 sheathing. This is the best warranty in the industry and is based on mean time before failure (MTBF) of over 250,000 hours. This is in comparison to typical stainless steel MTBFs of about 50,000 hours, which are typically three-year warranties.
Note that any company that provides a warranty, with stainless steel, above three years is not using the MTBF to base it and, as such, puts the product at risk. This means that the product will fail according to the MTBF statistics; the company may replace the heater on their dime, but does not cover the customer labor cost and risk of stopping a train.
Stainless Steel Flat Heaters
In addition to the NIBE Element Railway Solutions switch point heating technology design, the heaters are sheathed in a stainless-steel sheathing (316 grade or 321 grade).
While this solution is a much better solution than a Nikeloid alloy, it is not nearly as salt/weatherproof as the Monel 400 alloy heaters. This option does provide a less expensive option from the Monel 400 option.
More Info
Other Rail Heating Methods
While flat electric heaters offer optimal thermal conductivity and energy efficiency, NIBE controllers can support any electric resistive heater, including round tubular heaters.
Other rail heating technologies include:
Electric Round Tubular Heaters
Round tubular heating was the first electric switch heating method, developed in the 1970s. The heaters can generate wattages up to 600 watts per foot.
Disadvantages of electric tubular heating include:
- They burn extremely hot and have short operational lives—usually less than two years.
- The round shape limits thermal contact to the rail to 15% or less.
- Heaters are typically manufactured and delivered coiled—the heater has a metallic memory that curves the heater when applied to the rail, so perfect continuity to the rail cannot be achieved.
Blown-Gas and Open-Flame Heating
Blown-gas and open-flame heating were developed at the beginning of the 20th century, to replace smudge pot heating.
Blown-gas heating systems are powerful and can produce extreme heat. The heat is supplied via high-pressure air blowers.
Disadvantages of blown-gas heating include:
- Expensive initial capital cost.
- It is inherently dangerous in populated areas.
- The system is difficult to maintain—typically railroad staff will remove the ducting system at the end of the winter season and put it back on at the beginning to avoid excessive damage from the train.
Open-flame heating is another gas-powered method where a tube or runner with holes allows gas to flow down the length of the tube. The tube is then ignited, and the rail is heated through direct flame.
Disadvantages of the open-flame heating system include:
- It is inherently dangerous in populated areas.
- Wind can extinguish the flame.
Smudge Pot Heating
Developed in the 1800s, smudge pot heating is one of the original methods of heating switch points. Using kerosene or oil for fuel, individual smudge pots were placed on the side of the rail to produce heat. While antiquated, this method can still occasionally be found in use.
Legacy Heaters
Our sister company, Backer Hotwatt was established in 1952. It began with the manufacturing of one product, the open coil heating element. Since then, Backer Hotwatt products have expanded to include cartridge, air process, immersion, strip and finned strip, tubular and finned tubular, band, foil, flexible glasrope® and ceramic heaters. They are dedicated to the design and manufacturing of resistance heating elements for a variety of OEM and industrial applications. In addition, they can supply compatible accessory items which enable us to offer a complete heater system. We can source legacy heating elements through Backer Hotwatt for your needs. Click here to see Hotwatt's rail heating solutions.