Reduce Energy Costs by 80%+
Automated Rail Heating and Remote Diagnostics
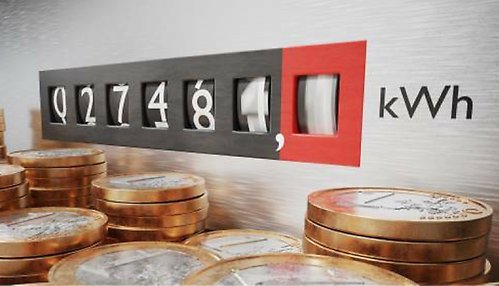
Of the $23 billion plus railways invest annually to modernize infrastructure, improve service, reduce congestion, and cut emissions, a significant portion is spent to restore, upgrade, and acquire new winter equipment and technology. In regions with harsh winter conditions, it is imperative to heat rail tracks to prevent ice and snow build up and maintain safe, efficient operations, an expensive proposition.
Traditionally, rail maintainers turn heaters on at the beginning of the winter season and run them continuously through spring until it is “safe” to turn them off. Or alternately, the train dispatch is augmented to allow control of the heaters remotely. Dispatch control can be very inefficient as the potential for human error could result in:
- Heaters being turned on too early
- Heaters being turned off later than needed
- Heaters being left on for extended periods of time
And worst-case scenario of all, the dispatcher forgets to turn the heat on at all, jeopardizing the train route, and potentially the dispatcher’s job! Automating rail heating control removes the risks posed by manual operations, improves energy efficiency, and eliminates the possibility of human error or forgetfulness.
Thanks to advances in automated electric rail heating technology—including dual element heating and Intelligent Weather Stations (IWS) paired with legacy systems—it is no longer necessary to run rail heaters continuously or rely upon dispatch control, both expensive and labor-intensive approaches.
NIBE Element Railway Solutions’ automated electric rail heating systems provide the hottest, on-demand track heating available—up to 600-watts per foot—all while significantly reducing energy consumption by up to 80% and higher!
Pairing advanced European rail heating technology with American ingenuity, NIBE offers customized solutions to keep your train operations running smoothly, economically, and efficiently. Designed and built in the U.S., our rail heating systems are robust, durable (the only heater with a 10-year warranty!) and offer excellent short- and long-term ROI.
Below you will discover comprehensive information about our automated electric rail heating solutions. Please feel free to browse through the various topics or click on a topic to go directly to that section.
How Automated Electric Rail Heating Systems Work
Automated rail heating systems use electric heaters strategically installed along the track, particularly at critical points such as switches, crossings, and inclines. These systems are typically controlled by weather sensors, rail sensors, and smart automation, allowing them to activate when temperature and moisture conditions indicate potential ice formation.
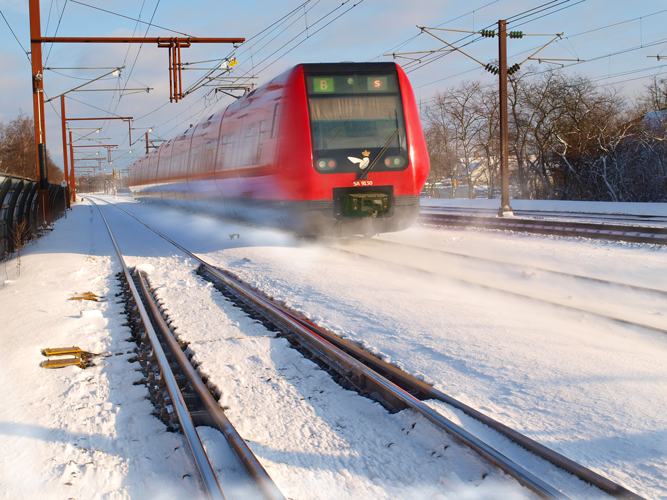
Key components of automated rail heating systems include:
- Heating Elements - Electric resistance heaters embedded in the tracks or mounted alongside switches.
- Rail Temperature - Redundant hot rail sensors and cold sensors are placed on the rail, opposite side of the heater, to measure accurate rail temperature.
- Snow Sensors - Snow sensors wayside and in the track to detect falling snow and trailing/blowing snow.
- Ambient Temperature & Moisture Sensors - Detect falling temperatures and the presence of moisture to trigger the system.
- Automated Controls - Smart algorithms optimize energy use, ensuring heating is activated only when necessary.
- Remote Monitoring Systems - 24/7 monitoring to alert rail operators of any issues in real time.
Benefits of Electric Rail Heating Systems
Automated electric rail heating systems offer various advantages, such as efficient heat application, reduced energy consumption, and proactive track heating during harsh weather conditions—eliminating risks of human error.
Systems typically include the following features, which offer a host of benefits.
Smart Temperature Control
- Traditional rail heating systems run continuously, consuming excessive energy.
- Automated systems utilize real-time weather data, temperature sensors, and predictive algorithms to respond quickly to changing conditions.
- On-demand heating reduces energy consumption significantly, with cost savings ranging from 50% to 80%, depending on system specifications.
Adaptive Power Modulation
- Instead of running heaters at full power, ideal systems will adjust power output based on actual rail temperature and snow accumulation.
- Using variable power control, energy consumption can be reduced by anywhere between 40-80%+.
AI-based Optimization
- Machine learning models analyze historical weather and rail conditions to optimize heating schedules.
- Remote monitoring and control reduces unnecessary energy use.
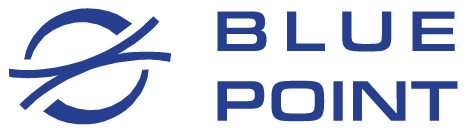
BLUE POINT Dual Element Rail Heating
Known throughout Europe for our advanced, automated rail heating systems, NIBE knew it was time to take rail switch heating to the next level in North America after the 2015 New England blizzard shut down passenger rail transit services. The failure of traditional track switch heating systems during this extreme weather event led the NIBE team to embark upon a quest to create the ultimate automated track switch heating system.
While the team's primary objective was to create an exceptional heat source that could manage extreme weather conditions, it became apparent that the need to monitor conditions and better control when and where heat is applied to the rail was also necessary. The team invented the world's first dual-element, pulse width modulated (PWM) electric rail switch heating system, BLUE POINT.
The dual-element heating system—used in conjunction with our patented PWM technology— has two heating elements on each rail. They work in harmony to achieve an effective wattage based on duty cycle. For example, dual 300-watt per foot heaters operating at 50% duty cycle provide an effective wattage of 300-watts per foot, whereas a 100% duty cycle produces a 600-watt per foot effective wattage.
The dual heaters are isolated from one another in the junction box so that if one heater fails the other will continue to work—a great redundant feature. The dual-element system is more efficient than traditional heating systems Pdf, 929 kB. and provides redundancy and operational flexibility. It is easy to change out a failed element which avoids unnecessary interruptions, reduces an operator’s workload, and extends the service life of the heaters.
A key advancement of the patented rail switch heating technology is that the dual heating elements are controlled by the BLUE POINT intelligent power controller. Using Pulse Width Modulated (PWM) technology the controller drives the dual elements heaters, automatically regulating the level of heat applied. The autonomous nature of BLUE POINT makes the switch heating system extremely dependable while providing redundancy.
The SCADA system runs, and is monitored remotely, continuously via the 24/7 Data Center. Communication is provided through a private cell modem to the NIBE Data Center. However, the BLUE POINT system does not require this communication to operate; the system sends detailed information back to the Data Center continuously for remote diagnostics and alerts.
While creating the hottest, more effective switch heating system was the NIBE team’s primary objective, an extraordinary “secondary” benefit has been realized. Several U.S. transit authorities that have installed NIBE’s automated electric rail heating systems have achieved a significant reduction in energy consumption and energy costs—up to 80% and higher.
The Genius of Pulse Width Modulated (PWM) Technology
BLUE POINT uses Pulse Width Modulated (PWM) technology to dial in the exact wattage needed to keep rails free of ice and snow. In extreme conditions, heat—as much as 600-watts per foot—is applied to switch rail and switch rods only when and where needed. The unique aspects of PWM include:
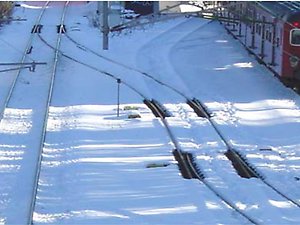
- The system will “dial in” the correct effective amount of wattage, 100-watts per foot up to 600-watts per foot.
- The system only applies extreme heat in extreme conditions for energy efficient heating operations.
- The heating elements are isolated so that a redundant path can operate one heater even if the other one fails.
- No trenching is needed to implement the dual element system, existing heater cabling can be used.
Combined with proactive 24/7 call center monitoring, remote diagnostics, and real-time alerts, the BLUE POINT/PWM system has already proven its mettle at several U.S. transit authorities, helping them to avoid costly delays, boost performance, and significantly reduce energy costs.
Benefits of Automating an Existing Rail Heating Legacy System
If you have an existing legacy system, there is a cost-effective way to automate rail switch heating without replacing your entire infrastructure. A conventional rail heating system typically runs 100% of the time during the winter months. But an Intelligent Weather Station (IWS) enabled system provides the same operational efficiency as the BLUE POINT system while saving 60% or better in energy costs.
NIBE’s IWS runs on a BLUE POINT platform and is attached to your system’s legacy controller which is driven through dispatch. Externally, temperature sensors are placed on the tracks. Automating your legacy system using NIBE’s IWS enables you to apply heat in response to changing weather conditions, rather than running heat continuously.
This cost-effective solution is easily implemented as no costly and time-consuming trench digging, cabling, or track work is needed (outside of placing rail temperature sensors on the rail). By utilizing your existing infrastructure, you can leverage the extraordinary efficiencies and cost savings enabled by NIBE’s advanced automated rail heating solutions.
Key components of the IWS rail heating system include:
- Weather Sensors: Measure temperature, humidity, snowfall, and wind speed in real-time.
- Rail Temperature Sensors: To allow precise heating profiles.
- AI & Predictive Models: The local SCADA system is augmented with remote historical weather data and machine learning to forecast heating needs.
NIBE’s Intelligent Weather Station automated rail heating system can achieve:
- 60%+ energy savings
- 30-50% lower maintenance costs
- 20-40% overall cost reduction